Tuğla Üretiminde Termik Santral Atığı
Puzolanik Uçucu Küllerin Değerlendirilmesi
Ayşen Çelen Öztürk
¹
Yapılan çalışmada, tuğla üretiminde ana malzeme
olarak kullanılan kilin, özelliklerini geliştirmek amacıyla, katkı
malzemesi olarak termik santrallerde yakılan kömürün katı atığı uçucu kül,
kullanılmıştır.
Daha önce yapılan çalışmalarda; uçucu küllerden üretilen cam-seramik
malzemelerin DTA ve X ışınları ile yapılan minerolojik analizlerinde yapının
amorf, ancak ısıl işlemler sonucunda cam-seramik dönüşümünün gerçekleşmiş
olduğu tespit edilmiş, kristal fazında MgAl²O4 (magnezyum alüminyum oksit)
ve FeMgSiO3(demir magnezyum silikat) yer aldığı görülmüştür[l]. Amorf
maddelerin kristalleşmesi nedeniyle egzotermik reaksiyon sonucu, sıcaklığın
açığa çıktığı saptanmıştır. Uçucu külün pişme sırasında açığa
çıkaracağı enerji ile normal pişme sıcaklığından tasarruf sağlanması
ve düşük sıcaklıkta sinterleşme, ekonomik üretimlere olanak sağlanabileceğini
düşündirilmektedir[2]. Bu konuyla ilgili yurt içi [3] ve yurt dışı [4] çalışmalar
mevcut olup araştırmalar halen devam etmektedir.
Kil ve uçucu kül kompozisyonuyla hazırlanan tuğla numunelerinin iki ayrı
sıcaklıkta sinterlenmesi sonucu, bünyesinde oluşan boşluklar sayesinde; ısı
iletkenlik değerinin azaltılması, su emme değerlerinin ve mekanik dayanımlarının
TS ve ASTM standartlanna uygun olması hedeflenmiştir.
l.Giriş
Yapılan bu çalışmada endüstriyel atık malzeme olarak, Tunçbilek termik
santral linyit kömürü puzolanik uçucu külü seçilmiş,Kılıçoğlu
kiremit-tuğla fabrikasından alınan kille belirli oranlarda kompoze edilerek
laboratuvar şartlarında farklı sıcaklıklar için sinterlenmiştir[5].
Kullanılan uçucu külün, tuğlanın fıziksel ve mekanik özelliklerini ne yönde
etkileyeceği araştırılmıştır.
Türkiye'de son yıllarda, endüstriyel atıkların değerlendirilmesi ve
kompozit malzeme üretiminde performansa olan etkilerinin araştırılması, gündemi
oluşturan önemli konulardan biri olmuştur. Termik santral, demir-çelik, bakır,
ferrokrom, gübre, kağıt vb. sanayi alanlarından elde edilen atık
malzemelere kullanım olanaklarının yaratılması çok yönlü yarar sağlayacaktır.
Özellikle konvansiyonel yapı malzemelerinin iyileştirilmesi yeni kullanım
alanları bulunabilmesini sağlarken, atıkların değerlendirilmesi; enerji
tasarrufu, ekonomi, çevre koruma ve doğal kaynakların daha akılcı kullanımı
gibi avantajlara neden olacaktır.
2. Deneysel Çalışmada Kullanılan Malzeme Özellikleri
2.1. Kil Hammadesinin Özelikleri
Puzolanik uçucu kül katkılı tuğla üretiminde, Kılıçoğlu Kiremit-Tuğla
Fabrikası kili kullanılmıştır. Kullanılan kil, tuğla üretimine uygun şekilde
öğütülmüş ve hazırlanmış olarak temin edilmiştir.
Tablo l.'de verilen Kılıçoğlu kil toprağı kimyasal analizine göre
kimyasal bileşim yüzdelerine bakıldığında, bu toprağın Montmorillonit
kil grubuna yakın olduğu ve tuğla üretimine uygun bir kimyasal bileşime
sahip olduğu görülmektedir[5].
Kimyasal Bileşim
|
%
|
SiO²
|
59.28
|
AI²O4
|
25,59
|
Fe²O³
|
5,42
|
Kızdırma Kaybı
|
9,7
|
Tablo 1- Kılıçoğlu Tuğla-Kiremit Fabrikası Toprağı Kimyasal Analizi
(Fab.tarafından verilen föye göre)
Elde edilen deney sonuçlarına göre üretilen uçucu kül katkılı ve katkısız
tuğlaların plastiklik suyu %33-42 arasında değişmektedir. Bu sonuçlar da Kılıçoğlu
kilinin üretim için uygun plastikliğe sahip olduğunu göstermektedir.
2.2. Uçucu Küllerin Özelikleri
Bu çalışmada Tunçbilek Termik Santralına ait "C" sınıfı uçucu
külü kullanılmıştır. Kullanılan uçucu küle ait kimyasal özelllikler
Tablo 2'de (29.6.1998 Termik Santrallar İşletme ve Bakım Dairesi Başkanlığı
Teknik Kontrol Lab. Müdürlüğü föyünden alınmıştır.) verilmiştir.
Bileşik
|
% Ağırlık
|
SiO²
|
56.47
|
AI²O³
|
22.88
|
Fe²O³
|
8,03
|
CaO
|
4.06
|
Na²O
|
2.14
|
MgO
|
1.92
|
K²O
|
1.69
|
SO³
|
0.9
|
TiO²
|
0.57
|
P²O5
|
0.22
|
Kızdırma Kaybı
|
0.91
|
Tablo 2- Tunçbilek Uçucu Külü Kimyasal Analizi.
3. Numune Üretimi
3.1. Tuğla Hamurunun Hazırlanması
Gerek deney aletlerinin olanakları, gerekse deney sonuçlarının güvenirliliği
açısından numune boyutlarının 40 x 40 x 160 mm. olması öngörülmüştür.
Böylelikle eğilme deneyi sonucunda iki prizma parçası üzerinde de basınç
deneyi yapılabilecektir.
Yapılan deneysel çalışmada, tuğla hamurunun şekillendirilmesinde, yarı
yaş şekillendirme yöntemi, ağızlıklı pres geliştirilerek kullanılmıştır.
Çalışma prensibi, sonsuz dişli bir burgu aracılığı ile sıkıştırılan
plastik hamurun, makinenin daralan ağız kısmına takılan ve istenen kesiti
veren ağızlıklardan şekillenerek çıkması esasına dayanır.
3.2. Numunelerin Pişirilmesi
Hazırlanan numuneler M.S.Ü Güzel Sanatlar Fakültesinin Seramik bölümündeki
fırınlarında pişirilmiştir. Fırın; maksimum ulaşabileceği sıcaklığı
1200°C olan, pişme süresi ve sıcaklığı manuel kontrol edilen elektrikli
bir fırındır. Pişme esnasında açığa çıkan gazların ortamı terketmesi
için baca ünitesi mevcuttur.
Pişme sıcaklığı olarak, 850°C ve 1000°C iki ayrı sıcaklık seçilmiştir.
Toplam pişirme süresi 8 saat olarak sıcaklık derecesine göre ayarlanmıştır.
Fırın içi tuğla numuneler koyulmadan önce ön ısıtma ile 100°C ye kadar
ısıtılarak zaman kaybı önlenmiştir. Fırın istenilen sıcaklığa eriştikten
sonra bir süre bu sıcaklıkta tutulup daha sonra ısıtma işlemi sona
erdirilmiş ve kendiliğinden soğumaya bırakılmıştır.
4. Deneysel Çalışma ve Sonuçlar
Uçucu kül katkısının, belirlenen oranlarda; %0, %5, %10, %15. %20, %30,
%40, %50 olarak, kile katılmasının tuğla üretiminde performansa etkisi, fıziksel
ve mekanik özelikler üzerinden araştırılmıştır. Üretilen numuneler üzerinde
sırasıyla;
- İç Yapı Analizi,
- Kuruma, pişme, toplam küçülmeler,
- Birim hacim ağırlık,
- Ağırlıkça su emme,
- Hacimce su emme,
- Eğilme dayanımı,
- Basınç dayanımı,
- Isı iletkenlik katsayısı-B. Hacim ağırlık ilişkisi.
deneyleri yapılmış ve sonuçları örnek sayısının aritmetik ortalaması
olarak verilmiştir.
4.1. İç Yapı Analizleri
Deneysel çalışmada üretilen tuğla numunelerin iç yapı analizleri, Anadolu
Üniversitesi Seramik Mühendisliği Bölümünün Araştırma Laboratuvarında
taramalı elektron mikroskobu (SEM) ile yapılmıştır. Elde edilen sonuçlar
katkı oranlarına göre sınıflandırılarak aşağıda verilmiştir.
Mikro yapı analizi sonucu elde edilen görüntülerde; uçucu kül miktarının
artmasıyla kil tabakaları üzerinde aglomere uçucu kül taneleri miktarı
artmaktadır. Aglomere tanelerde bulunan amorf bölgeler; içerdiği alkali
oksitlerinde etkisiyle tamamen erimiş, camsı yapıyı göstermektedir.
İç yapı analizlerine bakıldığı zaman:
- Katkısız ve %20' ye kadar olan uçucu kil katkılı numunelerde dane şeklinden
bahsetmek mümkün gözükmemektedir. Resim 1' de görüldüğü gibi katkısız
tuğla numunelerde gözle görünür porozite bulunmamaktadır.
- Kül katkısı arttıkça iç yapı analizlerinde görüldüğü gibi boşluklar
(porlar) fazlalaşmaktadır. Oluşan bu boşluklar çok farklı çaplara
sahiptir.
- %20 ile %30 uçucu kül katkılı numuneler arasında büyük bir porozite değişimi
görülmektedir.
- Resim 2.'de, %20 kül katkısından itibaren, farklı dane boyutları ve dane
şeklinin homojen olmadığı görülmektedir.
- Resim 3'de görülen, %30 kül katkı oranı ile hazırlanan tuğla
numunelerde yuvarlak daneler artmakta ve daneler küreselleşmektedir.
- Resim
4.'de %40 kül katkısından sonra porozitenin bir miktar azaldığı ve lifli yapının
arttığı görülmektedir.
- Resim 5'de görülen %50 kül katkılı tuğla karışımlarda süngerimsi bir
lifli yapının oluştuğu daha açık bir şekilde görülmektedir.
Gözeneklerin geometrisinde farklılıkların görülmesinin değişik
nedenleri vardır. Bunlar; pişirim sürecinde yeni silikat minerallerinin oluşumu,
hammaddelerden açığa çıkan gazların kısmi basınçları, sinterleşme sırasında
ara fazların ve cam fazının kinetiksel davranışlarıdır.
Çok sayıda yuvarlak mikroporların avantajı nemin kapilarite ile taşınım
imkanını gözlemlenebilir oranda yavaşlatmasıdır. Tuğla bünyesindeki
lamelimsi gözeneklerin yapı malzemesinin dona karşı dayanıklılığını
arttırdığı, C.Mayer ve Stegmüller tarafından kanıtlanmıştır [6].
4.2. Kuruma, Pişme ve Toplam Rötre Değerleri
Kurutma sırasında numunelerdeki suyun buharlaşması sonucu, taneler
birbirine zklaşmakta ve hacimsel bir küçülme olmaktadır. Kurutma rötresi
olarak isimlendirilen bu küçülme, karışımdaki kül oranının artışıyla
azalmaktadır.
Kül içerisindeki SiO2 ve Al2O3 gibi plastikliği olmayan fazlar, plastikliği
azaltmakta ve dolayısıyla kuruma rötresini de azalttığı düşünülmektedir.
Uçucu kül katkı oranı ile kuruma rötresi değerleri Şekil l'de verilmiştir.
Kuruma rötresi pişme öncesi bir fiziksel değişim olduğu için pişme sıcaklığı
ile ilişkisi bulunmamaktadır. Fakat tüm karışım oranlarının kuruma rötresi
değerlerinin birarada verilmesi amacıyla 850°C ve 1000°C'deki pişirilecek
numuneler aynı grafik üzerinde gösterilmiştir.
Uçucu kül katkı oranının artışıyla lineer olarak azalan kuruma rötresi,
%20 kül katkısında lineerliği bozarak önemli bir düşüş göstermekte ve
minimum seviyelere inmektedir.
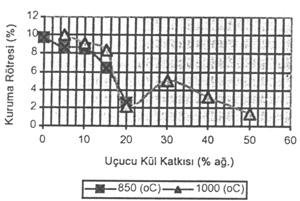
Şekil 1- Uçucu Kül Katkı Oranı- Kuruma Rötresi
İlişkisi
Şekil 2'de görülen pişme rötresi, kül miktarı arttıkça artmaktadır.
Bu artış, külün içerisinde bulunan yanmamış karbonun yanması sonucu açığa
çıkan enerji ve yine kül içerisinde bulunan Na2O ve K2O gibi alkali
oksitlerin sinterlemeye yardım etmesi ve külün puzolan özellikte olmasının
etkisi ile açıklanabilir.
Aynı kül katkı oranına sahip örneklerde; 850°C ve 1000°C'deki pişme sıcaklığında,
pişme küçülmesi değerlerinin aynı olduğu, sadece %15 kül katkı oranında
bir miktar farklılık gösterdiği, %20 kül katkı oranında yeniden 850°C ve
1000°C'de aynı değerleri taşıdığı gözlenmiştir.
Kilde bulunan alkali elementler ve kül içindeki puzolan mineraller, sıcaklığın
etkisiyle camsı sıvı faz oluşturmaktadır. Sıcaklığın artması ile artan
sinterleşme sonucunda sıvı faz miktarı da artmakta ve dolayısı ile pişme
küçülmesinde de artış meydana gelmektedir.
Sıvı faz sinterleşmesi oluşmadan önce, kompleks bir karışım olan
kilin 400-600 °C arasında kristal suyunu kaybetmesi, uçucu küllerin sıvı
faz oluşturması (killere göre daha az), uçucu küllerdeki karbonun yanarak
uzaklaşması numunelerde pişme küçülmesine neden olmuştur.
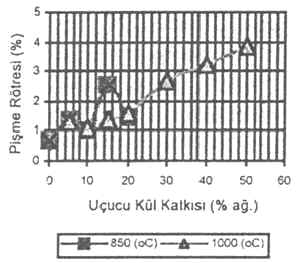
Şekil 2-Uçucu Kül Katkı Oranı-Pişme Rötresi
İişkisi
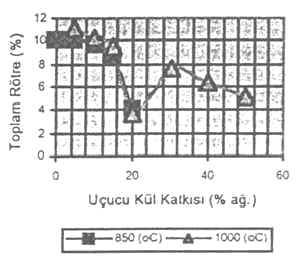
Şekil 3-Uçucu Kül Katkı Oranı-Toplam Rötre
İlişkisi
Şekil 3'de kuruma ve pişme rötrelerinin toplamı olarak ifade edilen
toplam rötre eğrisi incelendiğinde, kuruma rötresine benzer bir eğim görülmekte,
uçucu kül katkı oranmın artışıyla lineer olarak azalan toplam rötre, %20
kül katkısında lineerliği bozarak önemli bir düşüs göstermekte ve
minumum değeri almaktadır.
4.3. Su Emme Değerleri
Uçucu kül katkı oranı ve su emme değerleri Şekil 4.'de grafık olarak
gösterilmiştir. Bu grafıklere göre; su emme değerleri kül miktarı arttıkça
artmaktadır.
Kül içindeki uçucu maddelerin ve yanmamış karbon içeren organik fazların
sinterleme esnasında yanması ve CO ve CO2 şeklinde bünyeden uzaklaşması,
yapıda boşluklar oluşturmaktadır. Ancak göze çarpan bir bulgu da; kül
miktarının artmasıyla, pişme rötresinde artış olurken aynı zamanda su
emme değerlerinde de artış gözlenmesidir. Sinterlenmenin artması su emme özelliğini
düşürdüğü, standart seramik malzemelere nazaran su emme değerinin de
artması, yapıdaki oldukça fazla uçucu ve yanmamış karbon fazların
sinterleşme sırasında uzaklaşması ve yerlerinde boşluklar oluşması
sonucu ile açıklanabilir.
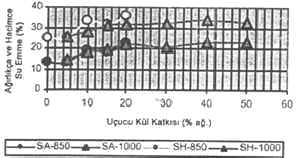
Şekil 4- Uçucu Kül Katkı Oranı - Su Emme Değerleri.
Sıcaklığın etkisiyle oluşan camsı faz kil miktarının düşüşüyle
azalacağından gözenekler tam olarak doldurulamamış ayrıca kül miktarına
bağlı olarak sinterleşme ile bünyeden gaz çıkışının artması bunu
desteklemiş ve su emme miktarının artmasına neden olmuştur.
4.4. Birim Hacim Ağırlık Değerleri
Şekil 5'de görüldüğü gibi; birim hacim ağırlıkları, uçucu kül miktarı
arttıkça düşmektedir. Numunelerin pişirilmesi sırasında; bünyelerindeki
karbonun oksitlenmesi, sülfatların gaz haline dönüşmesi, kil taneleri yüzeyine
absorbe olmuş suların ve kristal suların uzaklaşması, sonucu ağırlıklarında
bir azalma görülmüştür.
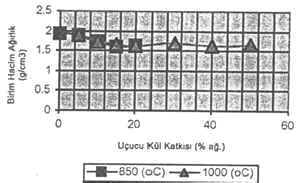
Şekil 5- Uçucu Kül Katkı Oranı - Birim Hacim
Ağırlık Değerleri.
Birim hacim ağırlığı, porozite (gözeneklilik) ve su emme değerleriyle
ters orantılı olarak düşmektedir. Şekil 6 ve Şekil 7'deki grafiklerde ağırlıkça
su emme ve birim hacim ağırlık değerlerinin ters orantılı olduğu görülmektedir.
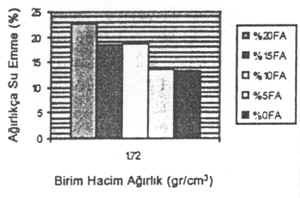
Şekil 6- 850°Cdeki Sinterlemelerde Birim Hacim
Ağırlık- A.Su Emme İlişkisi
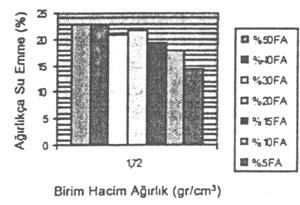
Şekil 7-1000°Cdeki Sinterlemelerde Birim Hacim
Ağırlık- A.Su Emme İlişkisi
Aynı kül katkısına sahip farklı pişme sıcaklıklarında (850°C ve
1000°C'de) birim hacim ağırlığının değişmediği ve her iki pişme sıcaklığında
da ağırlıkça su emme değerlerinin birim hacim ağırlığın artmasıyla
azaldığı, uçucu kül katkı oranının artmasına paralel arttığı gözlenmiştir.
4.5. Mekanik Dayanım Değerleri
Uçucu kül katkı oranı ile tüm mekanik dayanım değerleri Şekil 8'de
grafik olarak gösterilmiştir. Bu grafiklere göre; 850°C'deki pişirimlerde
artan kül oranı ile birlikte eğilme ve basınç dayanımları düşmüştür.
Kül miktarının artmasına paralel olarak artan gözenek miktarı, dayanım değerlerini
düşürmektedir.
850°C'deki sinterleşmede % 15 uçucu kül katkısmda eğilme ve basınç
dayanımlarında önemli bir artış görülmekte, %20 uçucu kül katkısında
dayanım değerleri azalmaya devam etmektedir.
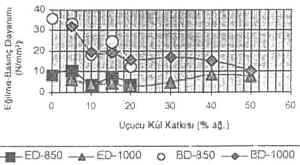
Şekil 8- Uçucu Kül Katkı Oranı-Mekanik Dayanım
İlişkisi.
1000°C'deki pişirimlerde basınç mukavemeti kül oranı arttıkça, hızlı
bir şekilde azalmaktadır. %15 kül katkı oranında eğilme ve basınç dayanımında
bir miktar artış gözlenmiş ve %40 kül katkısında eğilme dayanımı
maksimum bir değer göstermiştir. Bu maksimum değer; kül içindeki sertliği
yüksek fazların oranının artması sonucu, bir kompozit malzeme davranışı
olarak görülmektedir.
1000°C'deki sinterleşmede % 20' nin üzerindeki kül katkılarında basınç
dayanımı azalırken eğilme dayanımında artış gözlenmiştir. Bu aralıkta
basınç ve eğilme dayanımının ters orantılı olduğu görülmektedir. %50
kül katkısı miktarına gelindiğinde, artan porozite nedeniyle basınç dayanım
değeri eğilme değerine yaklaşacak kadar düşmektedir.
4.6. Isı İletkenlik Katsayısı -Birim Hacim Ağırlık İlişkisi.
Isı iletimi içyapı ile ilişkili olduğundan, birim ağırlığı az olan
malzemelerde ısı iletkenlik katsayısının da düşük olduğu görülmektedir.
Hafif ve içinde boşluklar bulunan malzemeler ısıyı en az geçirirler.
Bayındırlık ve İskan Bakanlığının 1999'da yayınlamış olduğu
"Mecburi Standart Tebliğ"in de verilen, TS 704 ve 705' e uygun dolu
ve düşey delikli tuğlaların birim hacim ağırlık değerlerine göre ısı
iletkenlik katsayıları Şekil 9' da verilmiştir[7]. Üretilen uçucu kül
katkılı tuğlaların deney sonuçlarına göre elde edilen birim hacim ağırlık
değerleri; 1.93, 1.89, 1.72 , 1.68 ve 1.59 gr/cm3 alınıp Şekil 9'da ki grafiğe
yerleştirilirse yaklaşık ısı iletkenlik değerlerinin 0,9 ile 0,7 W/mK arasında
değişeceği görülmektedir.
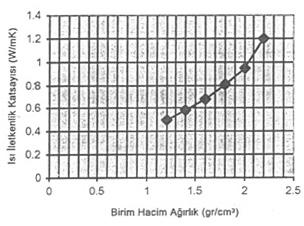
Şekil 9- Birim Hacim Ağırlık- Isı İletkenlik
Katsayısı İlişkisi.
5. Sonuçlar
Uçucu kül katkı miktarının artmasıyla kuruma küçülmesi azalmakta, pişme
küçülmesi artmaktadır. Toplam küçülmeye bakıldığında o da, uçucu kül
katkısıyla azalmaktadır. Bu da rötrenin azaldığını göstermektedir. Tuğla
üretiminde rötre istenmeyen bir olay olduğu için bu sonuç olumlu olmaktadır.
Su emme değerleri, uçucu kül katkı oranına paralel olarak artmakta, yüksek
sıcaklıktaki (1000°C ) pişirimlerde sinterleşmenin daha fazla olması ve gözenekliliğin
azalması ile düşük değerler almaktadır.
Kil-uçucu kül karışımlarında kül miktarınm artmasına paralel olarak
artan gözenek miktarı, dayanım değerlerini düşürmüştür. Genel olarak
mekanik dayanımlar, TS 7057 1985 [8] ve ASTM C216' daki standartların[9], üstünde
değerlere ulaşmıştır.
Elde edilen tüm değerlere göre; 24,4 N/mm" basınç dayanımı,
l,59gr/cm birim hacim ağırlık, yaklaşık hesaplanan ısı iletkenlik katsayısı
0,7W/mK, toplam rötre değeri %8,72 ve %18,38 ağırlıkça su emme ile,
optimum bileşimin 850°C de sinterlenen, kil ve %15 uçucu kül katkı oranı
olduğu sonucuna varılmıştır.
Kaynaklar
1. Ergüt Ş., Yılmaz Ş., Günay V., Özkan O.T., "Termik Santral Atık Uçucu
Küllerinin Karakterizasyonları, Seramik ve Cam Hammaddesi olarak Kullanım
Potansiyelleri", 8. Uluslararası Metalurji ve Malzeme Kongresi Bildiri
Kitabı. cilt 2, ss. 869-874, 1995, İstanbul. '
2. Duman N., Özgen S., "Termik Santral Atık Uçucu Küllerinin Karo Üretiminde
Değerlendirilmesi". 3. Seramik Kongresi Bildiri Kitabı, Geleneksel
Seramikler. cilt 1. İstanbul.
3. Öveçüğlu M.L.,Thijsen P. "Atık Uçucu Küller ve Yüksek Fırın
Curuflarından Elde Edilen Cam-Seramik Malzemelerin Özellikleri". 4.
Uluslararası Seramik Teknik Kongresi, ss. 124-130.1980 İstanbul.
4. Cumpston B., Shadman F., Risbud S. "Utilisation of Coal-Ash Minerals For
Technological Ceramics", J.Met.Sei. pp. 1781-84,27. 1992.
5. Öztürk Çelen A., "Tuğla Üretiminde Termik Santral Atığı
Puzolanik Uçucu Küllerin Değerlendirilmesi Üzerine Bir Araştırma."
Doktora Tezi, M.S.Ü.. 2001 İstanbul.
6. Baykara, M., (2000) "Seramik Yapı Malzemelerinde Mikro Yapının
Biolojik Boyutu" 2000'li Yıllarda Sağlıklı vc Güvenli Konutlar için
Tuğla-Kiremit Paneli, TUKDER, Ankara.
7. 'T.C Bayındırlık ve İskan Bakanlığı Mecburi Standart Tebliği".
Ankara 1999.
8. "Fabrika Tuğlaları", TS 705, 1985.
9. "Standart Specifıcation for Facing Brick". ASTM C 216. Annual Book
of ASTM Standards 97, vol. 16, pp.113-117.
--------------------------------------------------------------------------------------------------------------------
¹ Yrd. Doç. Dr. Osmangazi Üniversitesi, Müh. Mim. Fak., Eskişehir
|